News & Events | September 24, 2021
How creora 3D Max Solves the Conundrum of High-Stretch, Circular Jeans
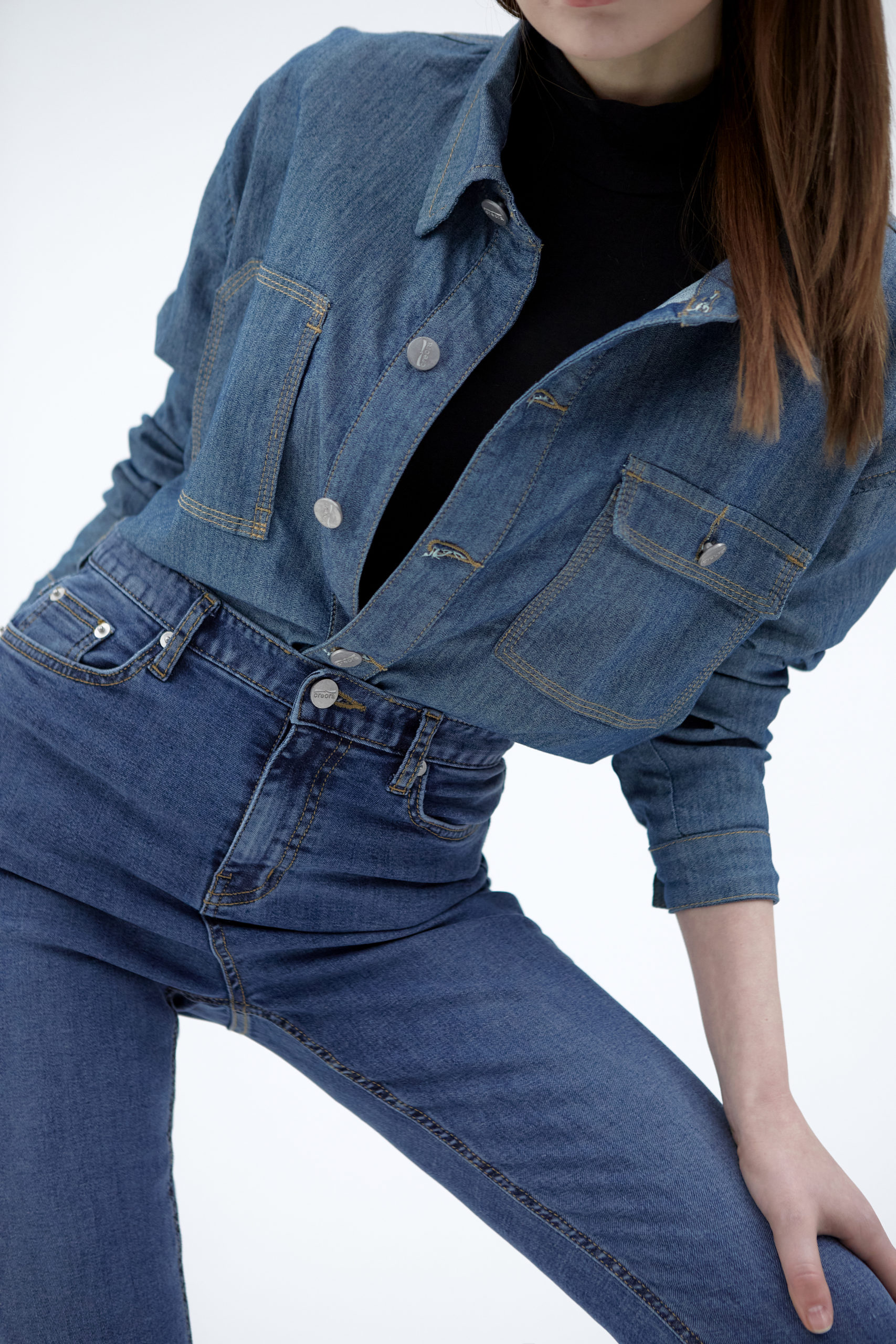
Denim is increasingly being held to circular standards as industry observers and consumers put pressure on brands and mills to reduce jeans’ weighty environmental footprint through reuse.
In response, firms are looking to develop denim that can be more easily recycled. And many are following Ellen MacArthur Foundation’s Jeans Redesign guidelines for recyclable denim. As of July, 94 producers had signed onto the program, including multi-billion-dollar retailers like American Eagle Outfitters, Gap, H&M, Levi Strauss & Co., Primark and Urban Outfitters, as well as upstream mill partners.
Jeans Redesign’s standards are meant to create jeans that are simultaneously more durable and easier to disassemble and recycle. Among the guidelines is a stipulation requiring denim to be made with a minimum of 98 percent cellulosic material, such as cotton, hemp, linen, lyocell or modal. This leaves just 2 percent of the content for stretch or synthetic material.
According to Jeans Redesign’s two-year progress report, keeping to this 2 percent limit has proven one of the top challenges for participants as retailers seek to serve consumers who are accustomed to high stretch and comfort. This demand for stretchy denim goes across styles and departments. Per NPD Group data, in the 12 months ended January 2020, sales of men’s jeans with stretch grew 40 percent. During the same period, women’s stretch denim was up 8 percent, and 88 percent of all women’s pairs sold in the previous year had some stretch element. Even trendy fits like mom jeans and wide legs often have some stretch to them.
According to Mike Simko, Hyosung global marketing director for textiles, high stretch and circularity can be compatible. The spandex manufacturer aims to help Jeans Redesign participants raise the number of jeans that fit the program criteria.
“Starting from the beginning, clearly people have demonstrated they want stretch,” Simko said. “The question becomes, how does the spandex industry react and make it so that you’ve got sustainability and circularity starting from the inputs.”
The industry desires denim that stretches by more than 50 percent with a maximum of 5 percent growth (aka sagging). Conventional spandex alone will provide stretch, but the recovery won’t live up to the standard—regardless of the percent of elastane in a textile. To achieve the recovery needed, the typical solution has been to mix polyester in with the spandex, creating a dual core that can more effectively bounce back. One solution combines cellulosic fibers with an elasticized polyester and elastane for recovery, but this added polyester content means that synthetic yarns make up 12 to 16 percent of a finished garment, preventing denim from meeting the 98 percent threshold for Jeans Redesign.
Hyosung’s creora 3D Max offers a solution to achieve a balance of stretch and recyclability, since it delivers a high performance stretch even as a small portion of fabric content. The yarn swaps the typical polyester core for spandex, creating a fully stretch material that retains the recovery properties of the polyester-spandex combination.
Aside from stronger recovery, 3D Max offers quality improvements. Polyester content doesn’t take dye the same way as cotton, leading to potential color defects such as white spots. In contrast, by eliminating the polyester and reducing synthetics to just 2 percent of a textile, creora 3D Max prevents irregular dyeing issues. Additionally, polyester doesn’t react as well to eco-friendly laser finishing processes that are growing in popularity.
Currently, 3D Max is being used by 17 different mills in markets like Pakistan, India, Vietnam, Turkey and China.
“Key denim brands are interested in environmentally-friendly treatments,” said Sam Chan, assistant sales director at Hong Kong-based Panther Denim. “Hyosung’s creora 3D Max enables us to produce a recyclable high-stretch and laser-friendly denim by eliminating the use of polyester.”
At Kipas, a creora 3D Max customer located in Turkey, half of the mill’s production currently uses sustainable materials. “Our partnership with Hyosung permits us to offer many sustainable solutions to our brand partners,” said Hurriyet Ozturk, development director at Kipas.
To improve the life cycle assessment of spandex, Hyosung has developed creora regen spandex, which is made of 100% reclaimed waste and has a 67 percent smaller carbon footprint than conventional elastane. The company has also introduced a bio-based spandex that trades fossil fuel inputs for corn, which pulls carbon from the atmosphere as crops grow. While there is not currently a bio-based or regen version of creora 3D Max, Hyosung is looking into these varieties.
Aiming to keep spandex out of landfills, studies are investigating the potential for biodegradable elastane. And Hyosung is part of an effort exploring enzymes that would break down stretch yarns.
“The spandex industry is on a journey,” said Simko. “Now, we’re not just looking at the inputs, but we’re considering end-of-life issues.”
Click here to learn more about Hyosung Performance Textiles.
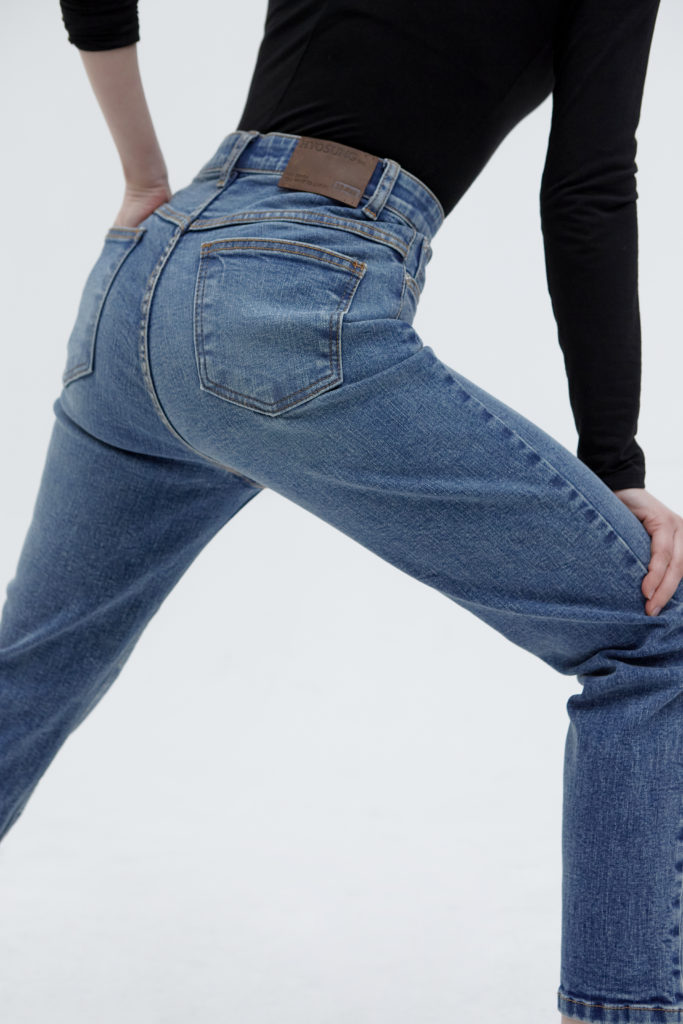
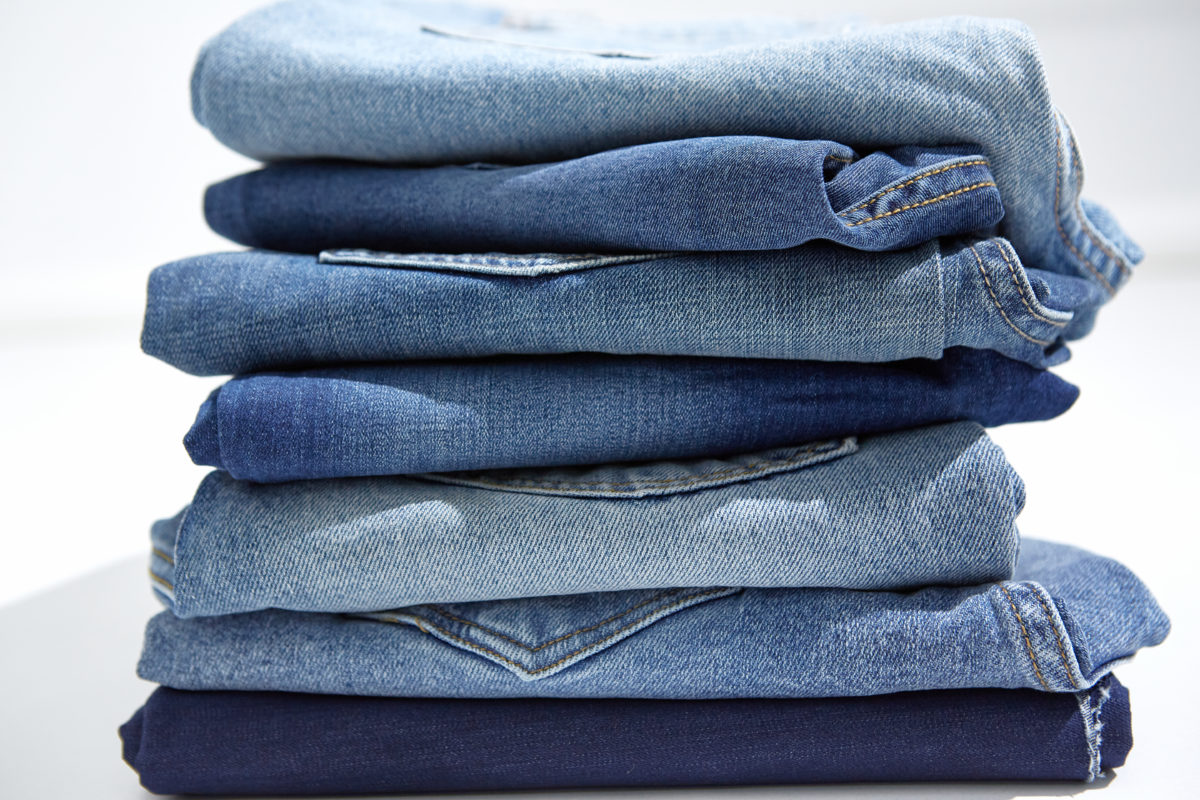
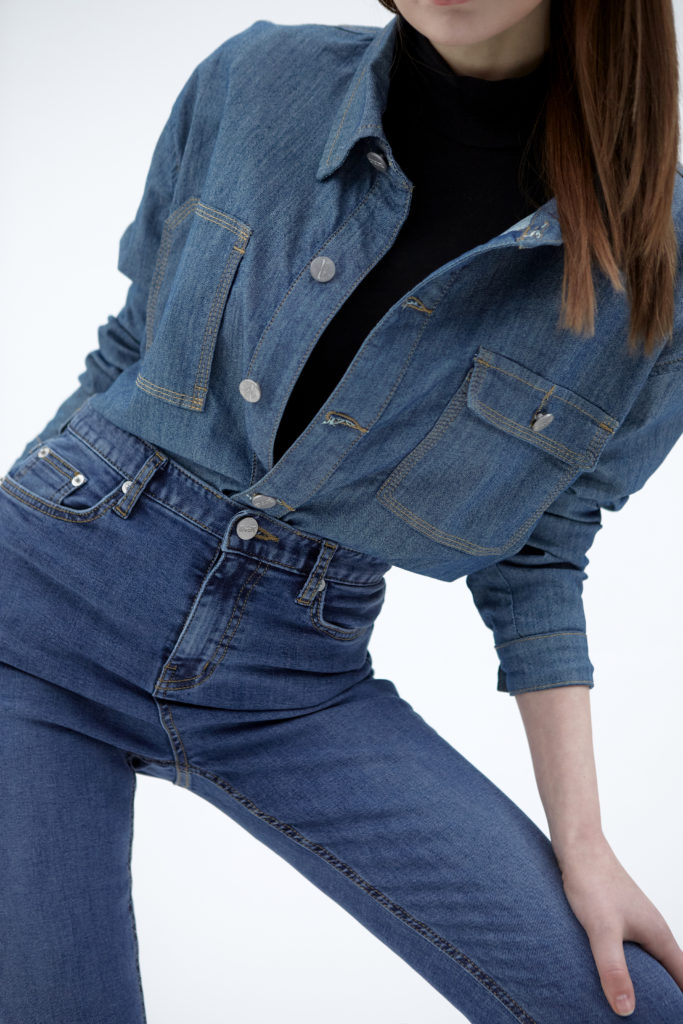