Stories | June 28, 2020
Designer Spotlight – Studio Eva X Carola
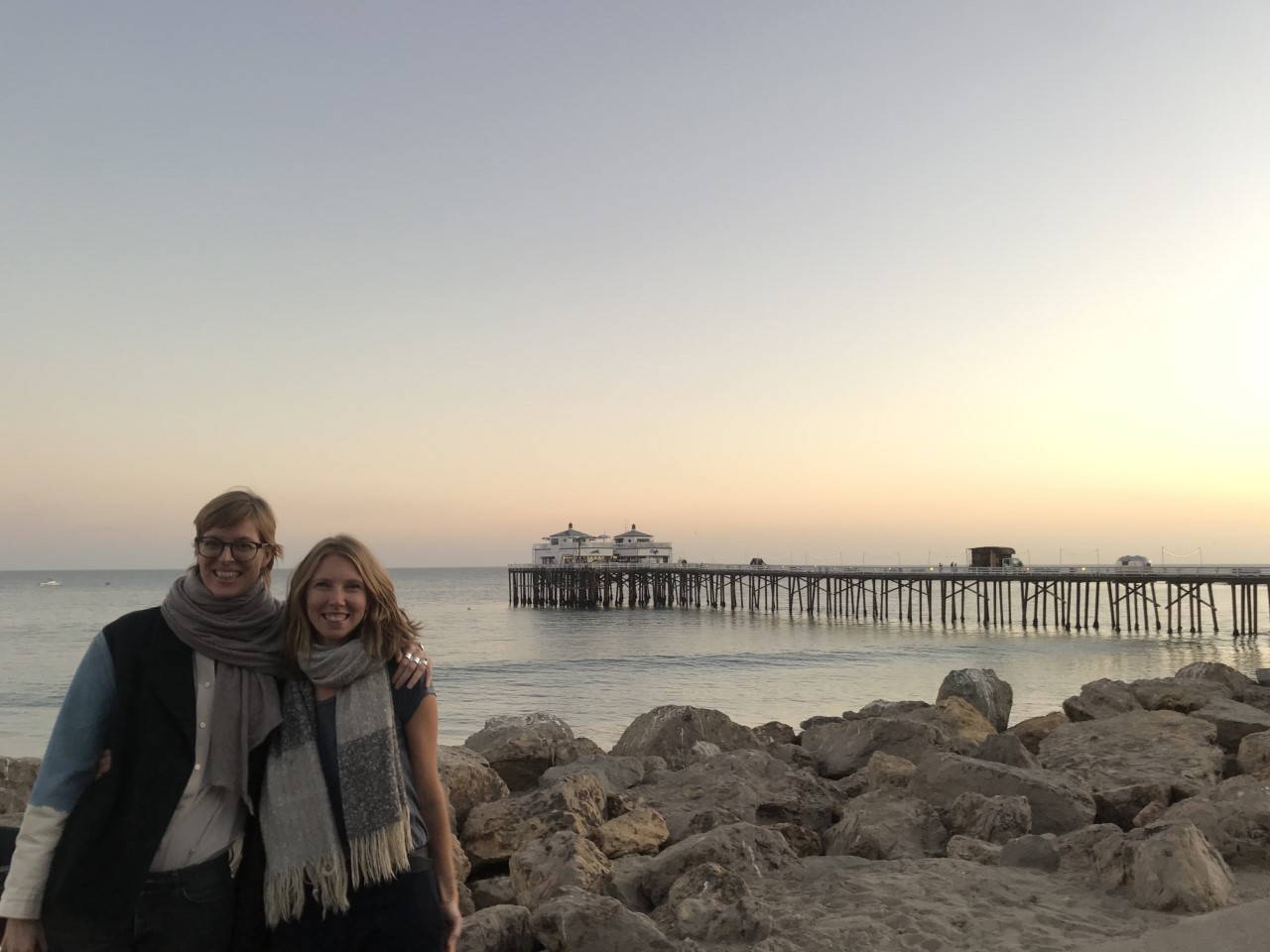
We are delighted to have Eva and Carola of Studio Eva X Carola join us for our first Designer Spotlight series!
If you are unfamiliar, Studio Eva x Carola is at the forefront of innovation in performance textiles, apparel, and footwear. Their expertise is in seamless and circular knit techniques and they are known for their unique way of making. If you have seen any of their unique performance pieces, you might call them visual pieces of art.
In our following conversation, Eva and Carola share how they met and formed Studio Eva X Carola. We get a peek into their unique design approach, discover what’s inspiring them, and what they’ve indulged in during COVID-19. We hope you enjoy.
How did the two of you meet?
We met in 1998 at university in Amsterdam where we studied Clothing Science at Mr. Koetsier, which is now called Amsterdam Fashion Institute. We became friends and participated in several projects together. In 2001, we went to New York together for a hands-on internship at a designer’s studio. After university we had our individual careers moved to different countries, but we always stayed in touch. We both worked a while at Nike, hence our passion for performance wear and seamless, circular knitting.
Do you have different skill sets that complement one another and if so, what are they?
Eva is very strong in her knowledge of yarns and has a lot of experience with working with the engineer next to the knitting machine. Carola focuses more on the design aspects and the creation of the technical files for the knitting machines. Both of us work in close alignment on the initial concept and creative direction. Each project brief and starting base is always made in close cooperation and both taking a role as creator and researcher. We also take critical analysis of any product or concept direction we decide.
When did you open your studio?
Our first collaboration was in 2014, when we were given the opportunity to research and develop textiles in the R&D center of Santoni Shanghai. We started exploring the possibilities within seamless knitting and learned how to engineer different elements in one production – known as an all-in-one process.
Can you elaborate a bit on what you call a ‘Different Way of Making’?
We feel we are making in a different way for several reasons:
1) The first reason is that we use a “reversed approach”. Designs are a result of testing and working with the machine, based on a specific concept. We select the yarns, the structures, and the patterns, and then we explore the results of combining these elements and adjust them during this exploration. Following this, the design is made and engineered on the body / product.
2) The second unique approach is what we call “from the yarn up”. Yarn selection is extremely important for us, along with creating the function we are trying to achieve. Products are created by knitting yarns that are carefully engineered into a tube. So rather than selecting a fabric that you cut and sew into a garment, a yarn is selected that is then knitted according to selected structures and machine setting, and seamlessly engineered into a tube – the tube is then made into a product with minimal construction steps. This is also why we really value partnerships with companies such as Hyosung creora® and platforms such as Woolmark.
3) Thirdly, seamless knitting is in a way a single piece bulk production, as each tube is created in one go followed by the next tube, it is possible to personalize each tube individually.
4) Maybe the 4th and main reason is the close alignment and partnerships we are creating across the supply chain. Each project is really created as a team and we see different ‘leaders’ in each stage. It’s a process by which we closely fine-tune each stage with a group of makers – from design, to yarn engineering, to machine technology.
Your knits are like pieces of art. Without giving too many of your secrets away, how do you approach specific seamless 3D designs?
We feel that everyone can make beautiful aesthetics but when it comes to functional textiles the focus seems to be often on the technical aspects. We are combining both by researching how to create the functional structures and then applying them to our aesthetic patterns. Thanks to seamless technology textures, function and colour can be allocated on a stitch-by-stitch level. This is how we can combine patterns with function. The 3D textures are a result of this, whereby different stitch combinations are allocated to different parts of the design.
How does sustainability come into play in your design?
Sustainability is a result of several decisions and considerations:
1) Products made on seamless technology can mean a reduction in waste due to the minimizing effect of the cut and sew process after knitting.
2) The consideration of recycled, biodegradable and dope dye yarns, such as Hyosung’s creora® eco-soft and creora® regen spandex are made with sustainability in mind.
3) We also strongly feel that making purposeful, beautiful and functional products will mean there is less need for lots of items in your wardrobe. Instead, you only have items that you can use / wear a lot and therefore there is less demand for “fast fashion”. In addition, at every stage, every decision is made based on consumer’s needs. We feel this results in higher value and longer-lasting products.
We are also very pleased with our newly established Material Experience Center powered by Santoni Shanghai. The center contains a display area, an advanced robotic research library and a making space. With this set up we also hope to further bring sustainability into our creative process and our partnerships with suppliers, brands and manufacturers. As design often leads up to 80% of sustainable issues, we hope with all the know-how and expertise available we are able to generate and promote smarter decisions from the offset. You can find a more descriptive presentation of the MEC at: https://docs.google.com/presentation/d/19tYTwqsgEFzAdJcWJ-Ki61G3oqtipKXMiRDiLNXF3g4/edit?usp=sharing
Are there any cool new innovations in textile development and/or design technology that have caught your attention?
Parametric design, for example using Grasshopper, is something we are interested to apply in our design process. Also, programs like Clo3D and Browzwear could be a solution to avoid translating 3D designs to 2D files. Thirdly, we are very interested in data-driven designs where the allocation of function is based on measured data. One of our first projects of data-driven design is our ‘engineered bra’. https://vimeo.com/237048659
What is inspiring you lately?
We always have a great interest in the development and possibilities of new yarns. We get inspired by new innovations and are keen to explore the functional aspects and test them on our machines. Lately, we have been working with waterproof yarns and developed a series of beautiful water-repellent materials. We are also inspired by how the current Covid-19 situation is leading to new opportunities. We see an increase in projects starting up around non-traditional textile areas. This gives us fresh insight and inspiration both for these industries as well as in more traditional textile areas.
What has been your biggest indulgence during COVID-19?
The extra kisses and cuddles from our children that we receive now having them around us 24/7.
If you were not designers, what would you be?
We are driven by the urge to make beautiful and purposeful items. So, if we were not designing, we would be crafting. But maybe this is a cheeky answer as we already feel we are as much crafting as designing. Therefore, it might not really be a change to what we are doing now.
For more information on Studio Eva X Carola, please visit www.evaxcarola.com.